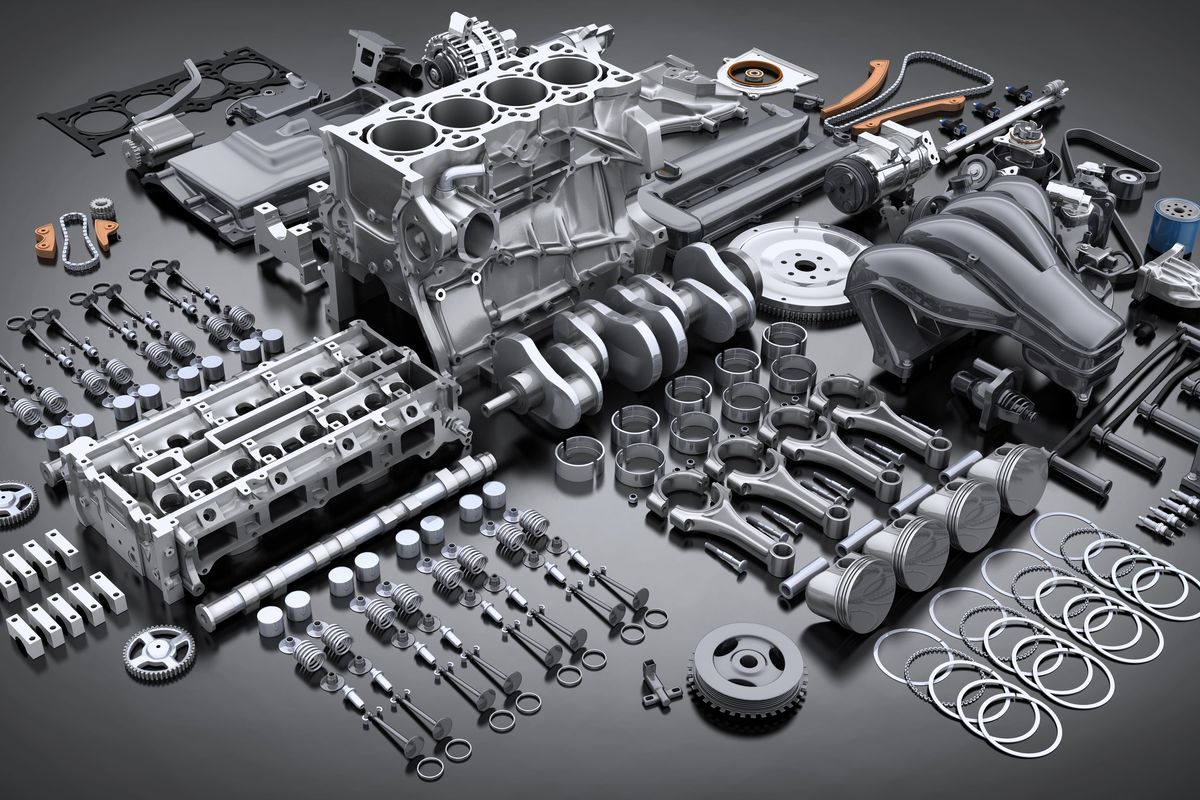
Penske Logistics Works with Robotic Processes to Deliver High-Performance Automaker Parts Management
An uninterrupted flow of parts is the lifeblood of just-in-time manufacturing. Using robotic process automation (RPA), Penske Logistics has reengineered a car manufacturer's legacy parts management process, significantly reducing the risk of supply disruptions that cause costly breaks in production.
In addition to saving millions of dollars in lost production time and increasing productivity, the RPA-based system is yielding data that sheds new light on the efficiency of the original equipment manufacturers' (OEM) parts pipeline. In collaboration with the manufacturer, Penske will use the data to capture more efficiencies and make the company's parts supply chain even more resilient.
Legacy Inefficiencies
RPA refers to software that enables bots to undertake basic applications typically performed by humans. The bots carry out this repetitive work much faster, and it releases employees to focus on other value-adding tasks.
However, Penske's RPA application is far from simple. "We aren't just using RPA to leverage some basic task automation. This was really looking at RPA in an end-to-end process redesign, fundamentally changing a critical process," says Brian Fidler, vice president of financial administration at Penske Logistics.
The legacy process had been in use for 15 to 20 years and relied heavily on manual interventions to track the inbound movement of parts such as engines and existing stocks for the carmaker.
The information was delivered in electronic and paper-based formats to some 120 analysts, who balanced the availability of parts — especially those critical to keeping assembly lines running — with each manufacturing plant's needs.
This finely tuned balancing act involves the supply of hundreds of thousands of parts to 26 plants. Moreover, the mix and volume of parts constantly change in line with the auto company's shifting needs and the varying requirements of each plant.
Driving Dramatic Improvements
Penske worked with the OEM for four months to redesign the established process.
As Fidler points out, by redesigning the process rather than trying to automate the original one, the team leveraged the full potential of Penske's RPA technology to transform the parts supply chain.
In the new, RPA-driven process, four bots interact with input data as well as the OEM's information system to populate the parts database. A fifth bot adds inputs from users. This sequence of interactions takes place continuously every 30 minutes.
The result is a parts management process that enables bots and humans to work together to deliver vastly improved service levels.
For example, the process is simpler and standardized. It replaces multiple sources of information with a single, consolidated report available to every authorized user. Retrieving information from the system is faster and more convenient.
The increased visibility into parts flows enables analysts to pinpoint potential parts shortages quicker and with greater precision. Also, the process is standardized across the facilities covered, while allowing for some customization so different plant requirements can still be accommodated. This is a vitally important advance on the legacy system's fragmented view of parts flows.
"The process mitigates the risk of disruptions by reducing the time taken to analyze flows and cycle parts, giving our team more time to make the right decisions," says Fidler.
These improvements translate an increase in productivity of up to 40% over five years — an almost tenfold return on the investment.
Unlimited Potential
While the project's returns are impressive, Penske expects them to increase even further as the 3PL in collaboration with its automaker customer explores ways to achieve efficiency gains in other operational areas.
For example, the manufacturer is pursuing an initiative to improve the movement of tractors and trailers through its freight yards. "We can leverage our parts management team at relevant locations to support this effort," says Fidler.
Another area that could benefit from the new system is transportation. Armed with a more granular picture of materiel flows into the OEM's manufacturing plants, Penske can carry out detailed analyses of carrier performance on key metrics such as on-time delivery.
RPA-inspired parts management automation also can yield strategic benefits. Analytics that draw on data from the system can help identify hidden costs in the supply base, insights that help the company monitor the efficiency of its business operations and redesign its supply chain if necessary. "There are lots of tentacles that we can build analytics around," notes Fidler.
From an industry perspective, the drive to apply RPA technology in the parts management space is part of a broader trend to digitalize supply chains, suggests Dave Bushee, vice president of logistics technology at Penske Logistics. "Intelligent automation could come next where we combine RPA with artificial intelligence," says Bushee.
Such advances can enhance control tower applications by, for example, identifying repetitive disruptions in the flow of parts and analyzing the impact on global operations.
Wide Horizons
The system's success provides a platform for other applications within and beyond the auto sector. "We feel strongly that within the automotive space, whether you are an OEM or a tier-one supplier, there is a need for the technology," says Fidler. There also are opportunities to improve materiel management in other industries using RPA, and Penske is actively exploring these options.
But regardless of the application, it is important to keep in mind that RPA is not merely a technology that can elevate the efficiency of basic, discrete tasks, Fidler emphasizes. RPA deployments offer the opportunity to rethink established processes and reorient them toward a digital future.
By "Move Ahead" Staff